How to create different types of chains through machine automation?
Posted on January 21, 2024
The automation process of producing different types of chains (such as roller chains, conveyor chains, decorative chains, etc.) usually includes the following main steps, which can be achieved through specially designed mechanical equipment and assembly lines:
Raw material preparation:
After strict inspection, the steel or required metal materials are cut or rolled into appropriate sizes according to the requirements of the chain specifications.
Stamping forming:
Continuous stamping of steel using a high-speed punch to produce components such as chains, pins, sleeves, and rollers. For roller chains, this step will separately stamp out the inner and outer chain plates, pin shafts, and rollers.
Heat treatment:
The produced parts may require heat treatment processes such as quenching and tempering to improve their strength, hardness, and wear resistance.
Mechanical processing:
For parts that require precision fitting, such as between rollers and sleeves, precision machining is carried out using a machine tool to ensure that the clearance between them meets the standards.
Automatic assembly:
By using automated assembly lines, various components are assembled, including steps such as embedding rollers into chain plates, installing sleeves, and threading them into pin shafts. This process is completed by machine hands or specialized assembly equipment.
Welding or cold heading connection:
Some chains require welding of connecting links, in which case automated welding robots will perform precise welding operations; For chain types that do not require welding, various parts may be fixed using cold heading or riveting techniques.
Surface treatment:
Automated electroplating, spraying, or other surface treatment equipment is used to provide anti-corrosion, aesthetic, and other effects to chains.
Testing and Quality Control:
The chain undergoes multiple inspections during the production process, including size, appearance, tensile testing, etc. Optical inspection equipment and mechanical testing machines are used to ensure product quality.
Packaging and logistics:
Finally, qualified chain products are packaged through automated packaging lines and classified, packaged, and transported according to order requirements.
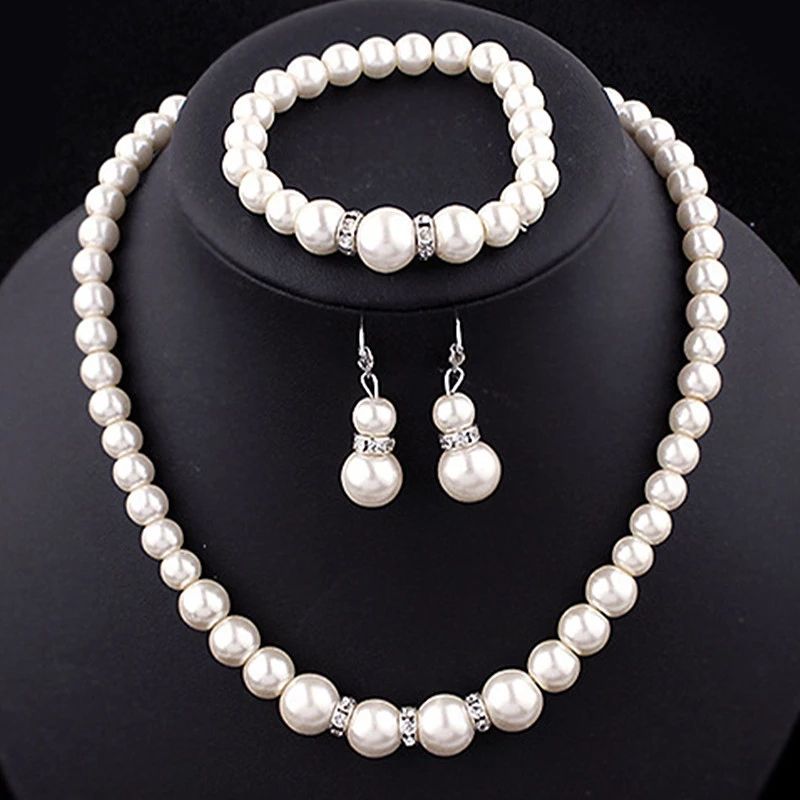
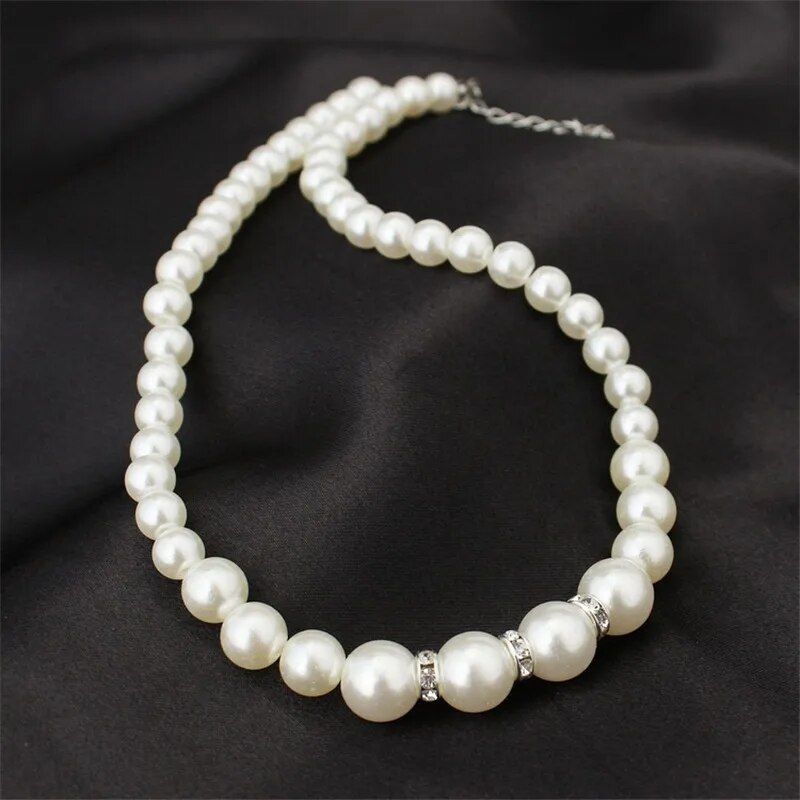
Wedding Engagement Women Simulated Pearls Jewelry Set Necklace Earrings Bracelets Fashion Jewelry For Lady Party Gift
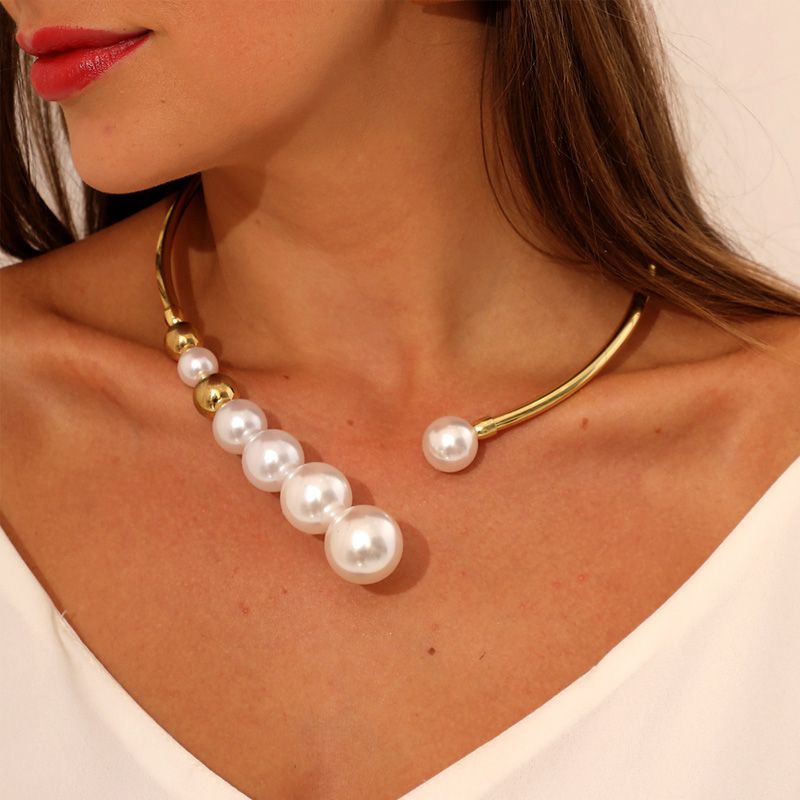
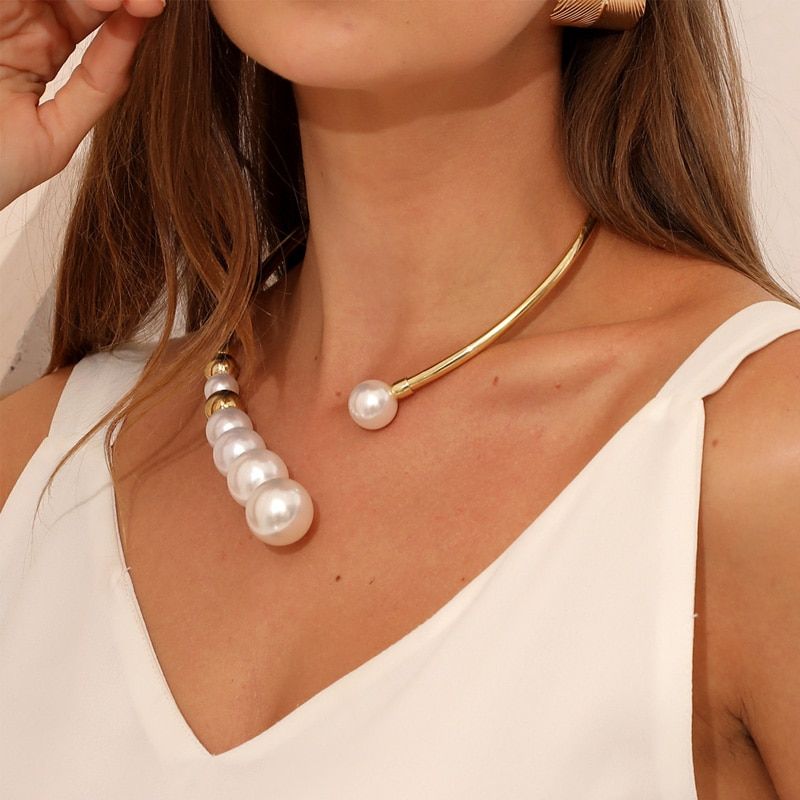
Pearl Necklace For Women Simple Versatile Golden Bead Opening Collar Exquisite Clavicle Korean Fashion Jewelry Gifts
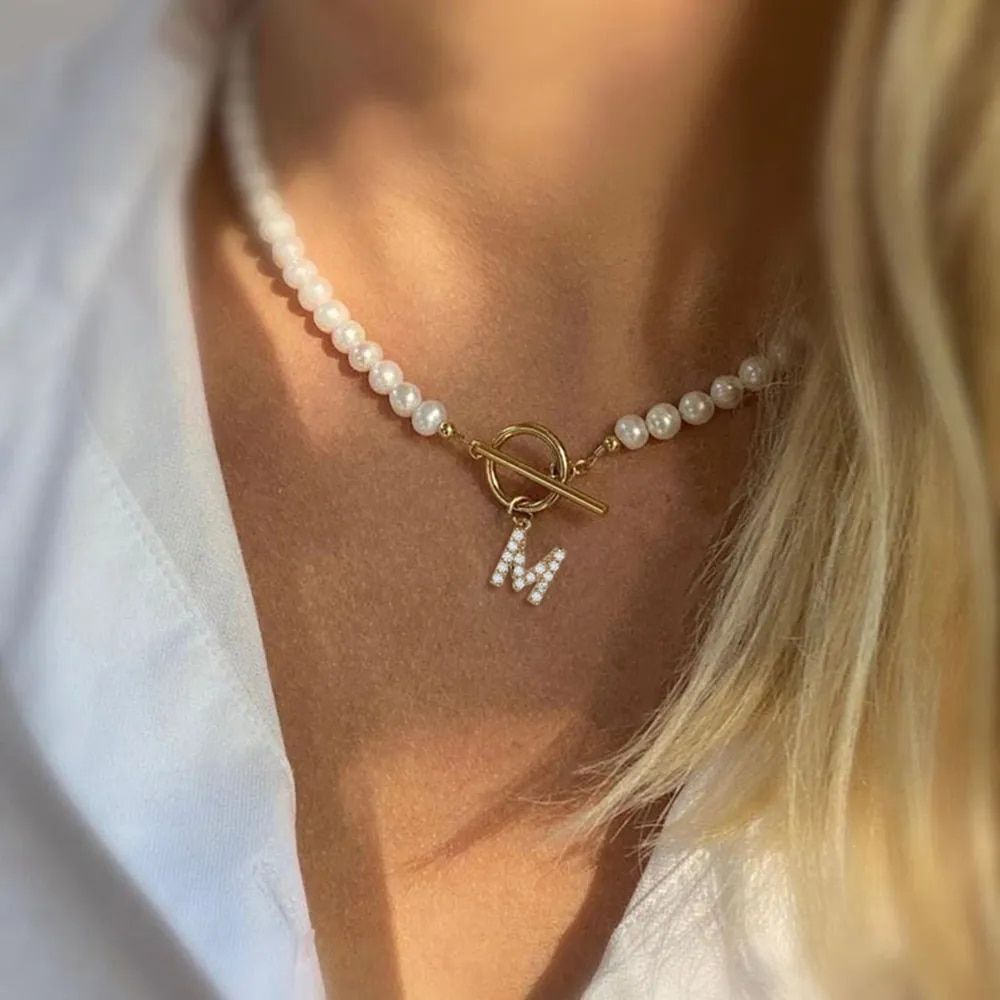
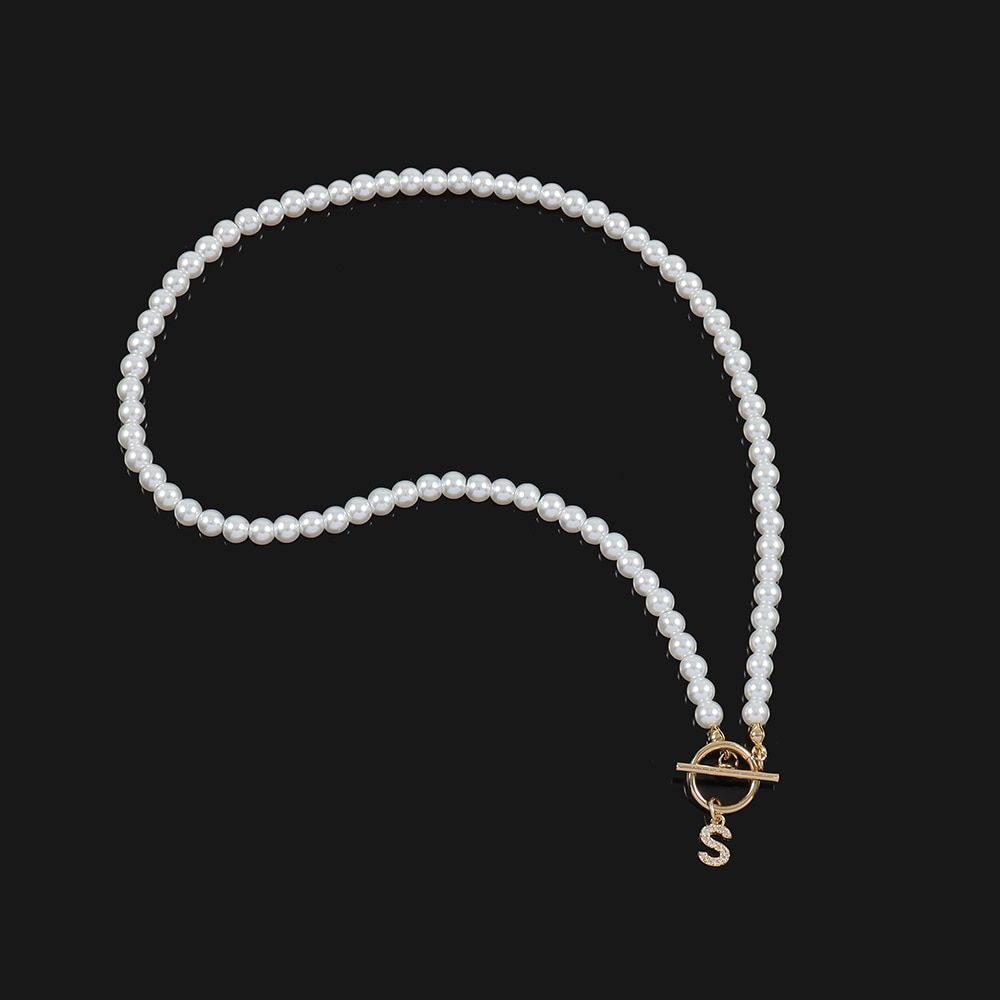
Classic Hot Initial Necklace Women A-Z Letter Pendant Toggle Clasp 6mm Imitation Pearls Necklace For Women Jewelry Gift
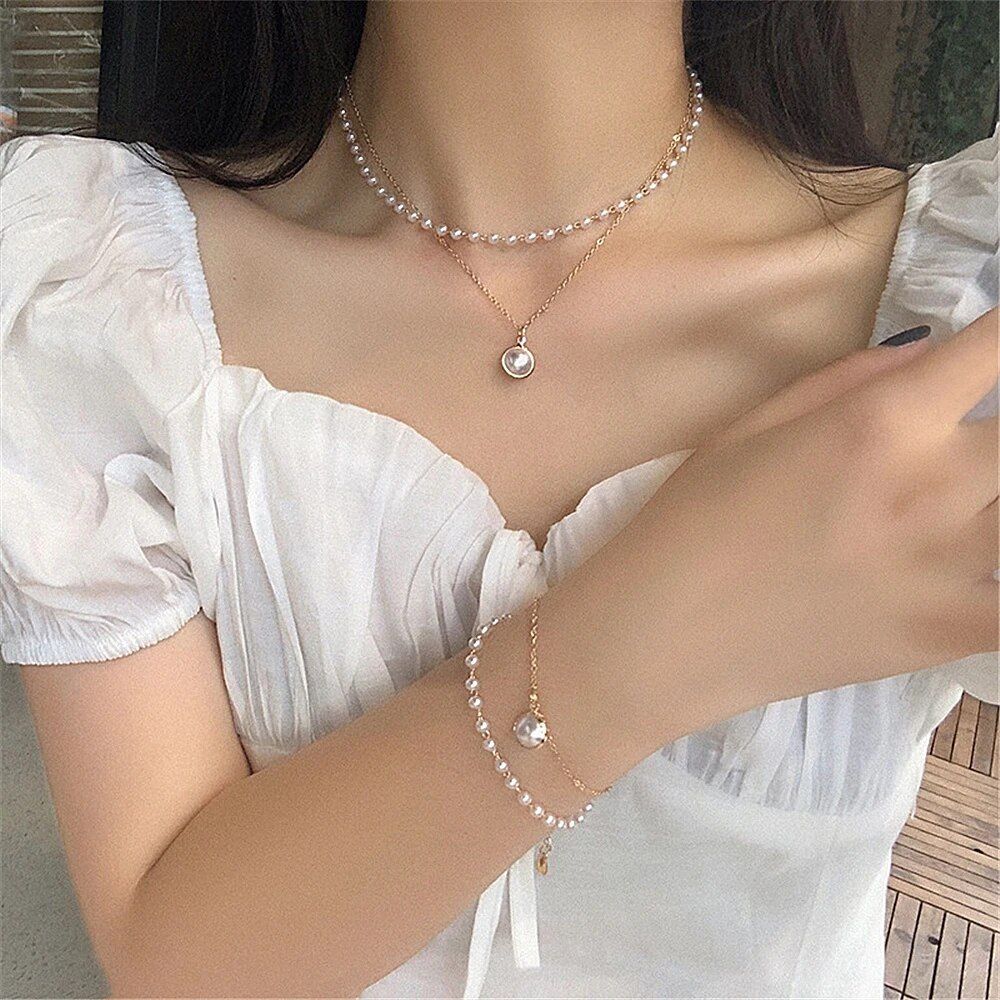
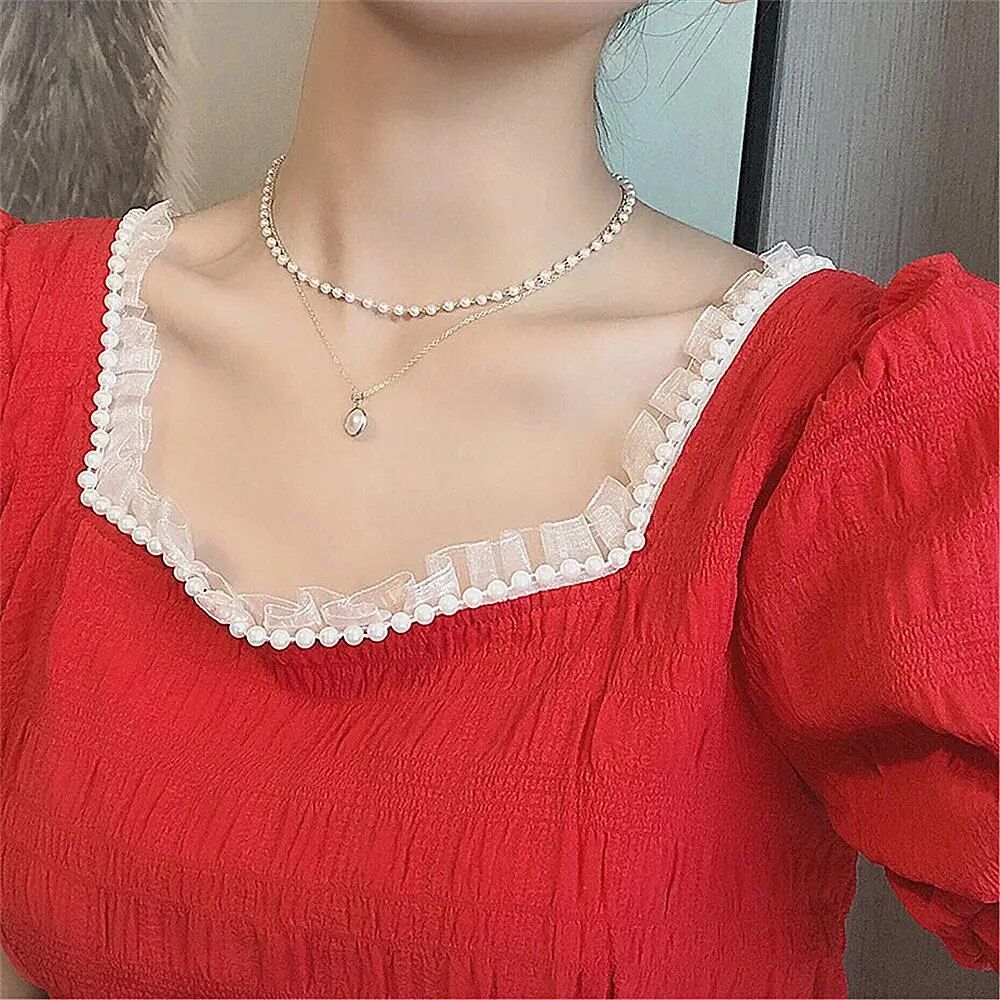
Fashion Retro Simple Pearl Choker Necklace Bracelet INS Fashion Double Layer Chain Pendant Jewelry for Women Girls Gift
Cart
0 Item(s)